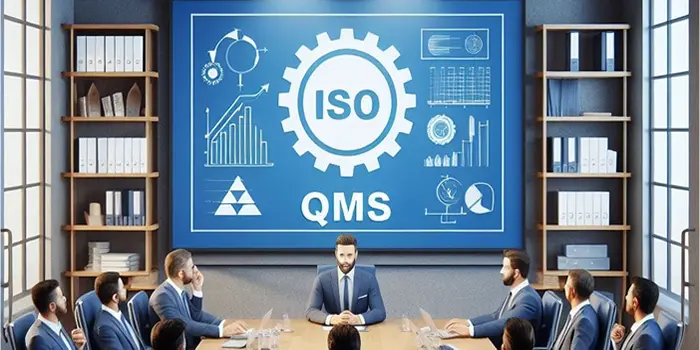
7 BASIC TIPS IN IMPLEMENTING ISO 9001 STANDARDS: MANUFACTURING SECTOR
Introduction
7 BASIC TIPS IN IMPLEMENTING ISO 9001 STANDARDS
Implementing ISO 9001 standards in manufacturing is more than just a compliance requirement—it’s a strategic move that can elevate your business operations to new heights of excellence. ISO 9001:2015 provides a structured framework for ensuring that every aspect of your business, from production to delivery, meets the highest quality standards. This blog will teach essential tips for effectively implementing these standards in manufacturing operations. From understanding the basics to fostering a culture of continuous improvement, these insights will help you navigate the journey towards quality excellence and customer satisfaction.
Here are essential tips for effectively implementing ISO 9001 quality standards in manufacturing business operations. Hence, 7 basic tips in implementing iso 9001 standards are discussed as follows:
1. Understanding the Basics
First, ISO 9001:2015 is all about quality management systems. It’s like the ultimate playbook for ensuring that everything you do in your business—from Sales and marketing to production and delivery—is top-notch.
2. Embrace the Quality Mindset
Okay, so before we get deeper into the discussion, let’s discuss the mindset. Maintaining ISO 9001:2015 standards is more than just ticking boxes on a checklist or establishing procedures and forms that might never be adhered to. It’s about ensuring quality is embedded into your organization’s work culture. It’s a commitment to customer satisfaction and excellence in everything you do. It’s a continuous thing – Keep churning out consistent conforming products /services that meet the client’s requirements while complying with the relevant statutory, regulatory, and legal requirements.
3. Get Everyone on Board
Next, teamwork makes the dream work, right? It would be best to have buy-in from everyone in the organization, from top management (MD/CEO) to line managers/supervisors and the staff on the factory floor. Ensure everyone understands the importance of quality and their role in maintaining those standards.
4. Documentation is Your Friend
Now, let’s talk paperwork. I know it’s not the most exciting part of the job, especially for the staff on the shop floor /operations, but trust me, it’s crucial. Document everything—from your processes and procedures to corrective actions and audits. This documentation helps the organization stay organized and provides evidence of its compliance with ISO 9001:2015.
5. Continuous Improvement
One of the most incredible things about ISO 9001:2015 is its focus on continuous improvement. It’s all about finding ways to do things better, faster, and more efficiently. Encourage your team to always be on the lookout for areas where you can improve and implement changes accordingly.
6. Training and Development
Knowledge is power. Ensure your team has the training and development they need to excel in their roles. Whether it’s academic competency, technical skills, or soft skills like communication and problem-solving, investing in your people pays off big time when it comes to maintaining quality standards.
7. Stay Engaged
Last but not least, stay engaged with the ISO 9001:2015 standard itself. Learn from the 7 basic tips in implementing ISO 9001 standards in this blog. Stay updated with any changes or updates, and make sure your processes and procedures reflect the latest requirements. Being proactive in this regard will save you many headaches down the line.
So there you have it—essential tips for maintaining ISO 9001:2015 quality standards in your manufacturing operations. Remember, it’s not just about compliance—it’s about creating a culture of quality that sets your organization apart from its competitors. Now, go forth and implement these tips!
Conclusion
Successfully implementing ISO 9001:2015 quality standards in your manufacturing operations is a commitment to quality that transcends mere compliance. It’s about embedding a quality mindset throughout your organization, ensuring every team member is aligned with your quality objectives. You can create a robust quality management system that meets and exceeds industry standards by following the tips outlined in this blog—embracing continuous improvement, prioritizing documentation, and staying engaged with the latest ISO updates. Ultimately, this commitment to quality will differentiate your business in the marketplace, driving customer satisfaction and long-term success. With these 7 basic tips in implementing ISO 9001 standards, you can be assured that it will affect your company positively if correctly applied
0 comments